By Damien Coleman
This month's Technical Focus article deals with the necessity to accurately diagnose faults on modern vehicles to avoid the needless replacement of expensive parts...
A 2005 Fiat Multipla with a 1.9 litre turbocharged compression ignition engine had been to an independent repairer because the malfunction indicator lamp was on and the vehicle was running on a limited operating strategy, often referred to as limp mode.
Further investigation found a fault code stored in the engine management control module:
- P0235 Turbocharger boost pressure malfunction
The customer was given a quote for the replacement of the turbocharger but asked for a second opinion.
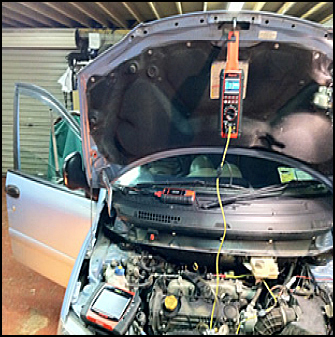
The turbocharger on this vehicle uses a type of technology referred to as variable geometry. It utilises vanes which can have their profile altered to vary the speed at which the exhaust gas hits the turbine shaft in the turbo.
The system operates on the Venturi principle, which results in the velocity of the exhaust gas increasing when the vanes are set to a narrow profile.
This restriction causes an increase in velocity due to the continuity principle in relation to dynamics of airflow.
A similar effect can be observed where two large buildings are situated close together and people walking between the buildings can experience an extreme windswept feeling.
The use of the variable geometry vanes on a modern turbocharger operate in a similar way.
A narrow profile (1) at low engine speed increases the velocity of the exhaust gas impacting the turbine shaft.
As a result, the turbocharger shaft will have an increase in speed and a greater boost pressure can be achieved at low engine speeds.
As the engine speed increases, the vane profile increases (2) and the increased volume of exhaust gas can then act on the turbine shaft.
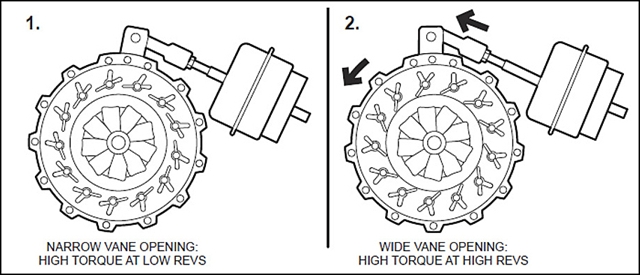
The advantages of this system are greater torque at low engine speed, more progressive boost pressure control and the option to fit a smaller turbocharger unit to the vehicle.
These units can be prone to carbon build-up, limiting the movement of the vanes. However, before condemning the expensive turbocharger unit, a diagnostic check was carried out on the system.
Diagnosing with a scanner and oscilloscope
I used the Snap-on VERDICT for this task as the tool is extremely flexible because it allows the connection of the scanner module (S3) and the oscilloscope module (M2) via Bluetooth. The seven-inch display device is more than suitable to display the data parameters alongside the oscilloscope trace without sacrificing detail.
Once connected to the vehicle the following data parameters were analysed:
- Key on, engine off with fault present
- Barometric pressure (mBar) - 1013
- Required turbocharger boost pressure (mBar) - 1056
- Actual turbocharger boost pressure (mBar) - 1179
It can be seen from this data that the turbocharger boost pressure is reporting a pressure greater than atmospheric pressure with the engine switched off.
This is incorrect. The engine control module runs a comparison between the barometric pressure and the boost pressure under certain conditions and if there is a correlation fault then a fault code will be logged in the system. The perfect condition for this is ignition key switched on and the engine switched off.
After analysing the data I decided to use a vacuum puller to reduce the voltage generated by the turbocharger boost pressure sensor.
By observing the serial data, I got the boost pressure sensor voltage to a point where the engine control module would allow the fault code to be cleared.
The image below shows the reduction in voltage required. The voltage was reduced from 2.2 Volts to 1.9 Volts.

The table below shows the serial data with a slight depression (vacuum) applied to the sensor:
- Key on, engine off with fault present
- Barometric pressure (mBar) - 1013
- Required turbocharger boost pressure (mBar) - 1029
- Actual turbocharger boost pressure (mBar) - 1136
A new turbocharger boost pressure sensor was fitted and the vehicle returned to normal operation with no fault codes stored. Incidentally, the sensor was approximately one tenth the cost of a new turbocharger!
Date posted: 12 May 2016